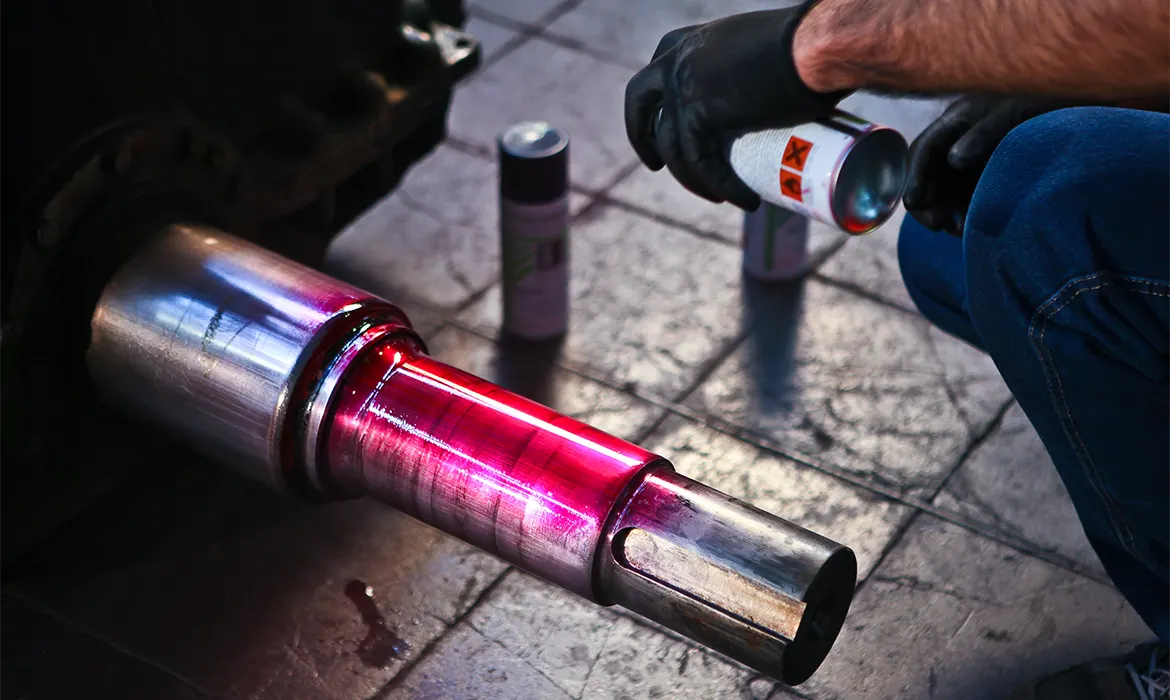
WHAT ARE PENETRANT LIQUIDS
News: Penetrant Liquids (or Penetrant Test PT control) are a method of non-destructive testing of materials; they give the name to the control technique itself. This method was introduced for the first time in the period before the Second World War; the authorship is officially attributed to the brothers Robert and Joseph Switzer who first conducted studies on PT control to improve its characteristics. The need to introduce a control practice different from the magnetic particle examination was linked to the introduction of light alloys (non-ferromagnetic materials) strongly in diffusion between the first and second half of the 1900s.
THE PENETRANT LIQUID METHOD
The testing method with penetrating liquids (PT) is based on the penetration of a liquid with certain characteristics of capillarity, viscosity, wettability and density within a discontinuity emerging on the surface. The non-destructive test with the penetrating liquid method is a procedure for inspecting the surface integrity with respect to defects emerging on metallic materials. Typically the penetrant is red (color linked to the presence of aneline), while the detector (based on amorphous silica) is white. This chromatic difference makes it possible to make any emerging defect easily visible.
FLUORESCENT PENETRANT LIQUIDS
In addition to the classic method of control with red penetrant, there are other types of penetrant with fluorescent pigment, which can be used with the aid of ultraviolet light. greater propensity of the human eye to see fluorescence in a darkened environment. Penetant liquids also exist specifically designed for application at high temperatures; they typically come in the form of waxes. Their application is not very developed and widespread due to the difficulty of performing the method
THE ADVANTAGES OF THE PENETRANT LIQUID METHOD
The advantages of a non-destructive testing carried out with the penetrating liquid method are many. First of all, its field of application is very broad. The method can be used:
- on all materials, metallic and not;
- independent of the geometry of the pieces to be examined;
- to highlight emerging discontinuities in surfaces, even of very small dimensions;
Furthermore, in the case of applications with portable kits, the PT method is relatively simple to use and with low costs. In any case, it is essential that the execution is carried out only by personnel certified at least 2nd level according to UNI EN ISO 9712.
THE DISADVANTAGES OF THE PENETRANT LIQUID METHOD
Given the high capillarity and the penetrating power of the penetrating liquids, it will be particularly difficult, if not impossible, to check surfaces with a porous structure. Furthermore, compared to other non-destructive tests, a strong limitation of this type of control is the impossibility of detecting "open" discontinuities (which cannot be defined as having a capillary structure and which would thus allow the penetrant to escape upon removal). Even the discontinuities located "under the skin" (immediately under the surface layer) or inside the piece under examination will be invisible. Precisely for what has been said, the method of penetrating liquids is defined exclusively as "surface control". A further limitation to the method is represented by the examination of plastic materials that could react with components of the penetrant by melting or giving rise to a principle of corrosion that would invalidate the control.
HE REFERENCE STANDARDS FOR PENETRANT LIQUIDS
All the non-destructive tests carried out by Punto Netto are required to satisfy a series of indications contained in national, EU and foreign regulations. The main regulatory sources for the control of penetrating liquids are the UNI (Italian National Unification Organism), the ISO (International Organization for Standardization), the American ASME (American Society of Mechanical Engineers) and ASTM International (American Society) regulations. for Testing and Materials).
Here are some standards used by PUNTO NETTO:
• UNI EN ISO 9712 "Non-destructive tests - Qualification and certification of personnel assigned to non-destructive tests"
• UNI EN ISO 3452-1 / 2/3/4/5/6 "Non-destructive tests - Examination with penetrating liquids"
• UNI EN ISO 5817 "Welding - Joints welded by fusion of steel, nickel, titanium and their alloys (excluding energy beam welding) - Quality levels of imperfections"
• UNI EN ISO 23277 Non-destructive control of welds - "Control of welds by penetrating liquids" - Acceptable levels
• UNI EN 10228-2 "Non-destructive testing of steel forgings - Control with penetrating liquids"
• UNI EN 1371-2 "Foundry - Control with penetrating liquids - Part 2: Lost wax castings"
WHAT ARE THE PHASES OF A NON-DESTRUCTIVE TESTING WITH PENETRANT LIQUIDS
The examination is generally carried out following the steps listed below:
1) Preparation and preliminary cleaning:
All contaminants, such as scale, rust, oil, grease or paint, must be removed, using mechanical or chemical methods, or a combination of both, if necessary. Preliminary cleaning must ensure that the surface to be examined is free from contaminating residues and that it allows the penetrating liquid to enter all discontinuities. The clean area must be large enough to prevent interference with the areas adjacent to the one that is actually to be examined. At the end of the preliminary cleaning phase, the parts to be tested must be carefully dried so that no traces of water and solvents remain in the discontinuities.
2) Application of penetrant liquid:
The penetrant liquid can be applied to the part to be tested by spraying, brushing, wetting, ablution or immersion. The penetrant liquid must remain on the test surface for the entire penetration time. The correct penetration time depends on the peculiar properties of the penetrant liquid, the application temperature, the material of the parts to be examined and the discontinuities to be detected. The breakthrough time must be between 5 and 60 minutes and must not be less than the time recommended by the manufacturer for the required sensitivity. The penetration time must be recorded in the inspection report
3) Removal of excess penetrant:
The application of the removal agent must be such that the penetrating liquid remains in the discontinuities. Various removal methods can be used, such as:
Water: Excess penetrant should be removed by washing (rinsing), dipping or scrubbing using water.
Solvents: Excess penetrant should be removed, first, using a clean, lint-free cloth lightly moistened with solvent. When removing excess penetrant, the surface under examination should be checked for any residue of penetrant.
4) Application of the detector:
The detector must be kept in homogeneous conditions throughout its use and must be applied uniformly on the surface under examination. The application of the detector must be carried out as soon as possible after the removal of excess penetrating liquid.
5) Inspection:
For the inspection, the illuminance on the test surface must be 500 lx or greater. The indications produced by the liquid penetrant method may provide limited information on the shape and size of the discontinuities. In some cases it may prove advantageous to carry out the first check immediately after applying the detector or as soon as it has dried. This facilitates a better interpretation of the indications. After the revelation time has elapsed, the final inspection must be carried out. Inspection aids such as magnification tools can be used
6) Registration of any defects:
Registration can be done by any suitable method, for example written description, sketch or photograph.
7) Final cleaning:
After the final inspection it is necessary to carry out the cleaning of the part in those cases where the products used for the examination with penetrating liquids could interfere with the subsequent operation or service needs